Durchbruch in der Konstruktion von Gussbauteilen
Bislang nutzt die Industrie bei der Herstellung von Gussbauteilen verschiedene Softwaretools zu den einzelnen Produktionsschritten. Ein Team aus Forschenden hat diese nun zu einer Softwarekette kombiniert. Das Ergebnis könnte die Konstruktion von Gussbauteilen revolutionieren.
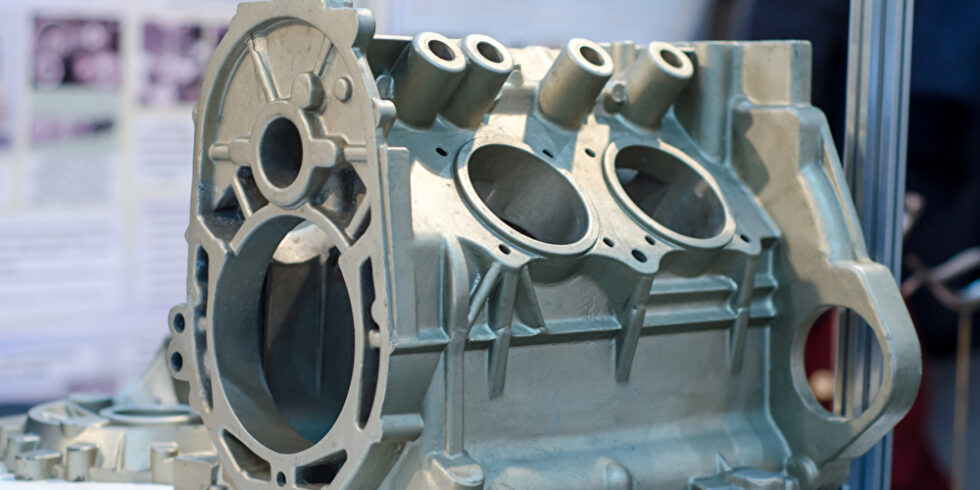
Besonders in der Automobilindustrie, Maschinen- und Schiffsbau sowie Medizintechnik kommen Gussbauteile zum Einsatz.
Foto: panthermedia.net/Oleksandr_UA
Gussteile gehören zu den besonderen Bauteilen. Sie werden in der Regel aus einem Stück gegossen und bestehen nicht wie andere Komponenten aus verschiedenen einzelnen Teilen. Als Basismaterial dient dafür meist flüssiges Metall. Solche Gussteile kommen vor allem in der Automobilindustrie vor, zum Beispiel sind sie Teile des Motors, des Fahrwerks sowie der Karosserie. Aber auch im Maschinenbau sind Gusskomponenten ein wichtiger Bestandteil. Zahlreiche große und kleine Geräte beinhalten gegossene Teile, auch wenn das auf den ersten Blick nicht sichtbar ist. Das gilt zum Beispiel ebenfalls für Gebrauchsgegenstände im Alltag wie Kaffeemaschinen oder Waschmaschinen. Dazu kommen dann noch Branchen wie der Schiffsbau, die Medizintechnik, die Luft- und Raumfahrt und die Schienentechnik, die Gussteile in unterschiedlichen Zusammenhängen einsetzen.
Das Besondere an Gussbauteilen: Sie müssen verschiedene Eigenschaften erfüllen, zum Beispiel eine bestimmte Struktur und Festigkeit aufweisen. Auch die Frage der Gießbarkeit ist relevant, ebenso Gewicht und die Eignung für den Leichtbau. Daraus ergibt sich automatisch, dass ein gewisser Aufwand notwendig ist, um qualitativ hochwertige Gussbauteile zu produzieren. Hinzu kommt noch die Anforderung, die Herstellung möglichst effizient und kostengünstig zu gestalten. Das Forschungsprojekt „DNAguss: durchgängige numerische Auslegung entlang der Prozesskette von Gussbauteilen“ unter der Leitung des Fraunhofer-Instituts für Betriebsfestigkeit und Systemzuverlässigkeit LBF in Darmstadt konnte nun einen Durchbruch erzielen, um dieses Ziel zu erreichen.
Softwarekette soll Konstruktion von Gussbauteilen revolutionieren
Die Forschenden verknüpften einzelne Softwaretools, die im Rahmen des Produktionsprozesses von Gussteilen verwendet werden, zu einer sogenannten Softwarekette. Das Ergebnis verschiedener Tests zeigte, dass sich einerseits die Gestaltung der Struktur verbessern, das Gewicht reduzieren ließ und sogar die Kosten in der Herstellung reduziert werden konnten. Die Qualität des Gussteils blieb dabei gleich, es gab dahingehend keinen Nachteil.
Im Rahmen des Forschungsprojektes kombinierte das Team ein Finite-Elemente-Programm, zum Beispiel Permas, eine Gießprozesssimulation wie Magmasoft und ein Programm zur Formoptimierung, in diesem Fall FEMFAT. Darüber hinaus erstellte das Team auf Basis der Daten von Magmasoft sowie von Versuchs- und Metallographie-Daten eine Korrelationsgleichung, welche die lokale Schwingfestigkeit in Abhängigkeit von der lokalen Gefügezusammensetzung bestimmt. Sie machte die gezielte Optimierung des Gewichts möglich und sorgte gleichzeitig dafür, dass die Betriebsfestigkeit des Bauteils ebenfalls sichergestellt wurde.
Softwarekette senkt Kosten bei gleicher Qualität
Dabei berücksichtigten die Forschenden ebenfalls eine lokale Materialdefinition. Denn bei Bauteilen mit unterschiedlich dicken Wänden entstehen automatisch auch unterschiedliche Geschwindigkeiten beim Abkühlen des Gussteils. Ist die Wand dünner, ist die Abkühlzeit auch deutlich kürzer. Das bedeutet gleichzeitig, dass ein Gefüge mit hoher Graphitausscheidungsdichte entsteht. Ein solches Bauteil ist durchaus belastbarer als andere. Es gibt noch einen weiteren Faktor, der die Beanspruchung beeinflussen kann: das Ferrit-/Perlit-Verhältnis. Es wird auch als Schwarz-Weiß-Gefüge bezeichnet. Schwarz steht dabei für Perlit und Weiß für Ferrit. Perlit enthält bereits etwas Kohlenstoff, während Ferrit reines Eisen ist. Damit ein Bauteil sehr belastbar wird, sollte der Anteil des Ferrits gering ausfallen.
„Die Projektergebnisse zeigen, dass durch die Verkettung fortschrittlicher Softwaretools die Konstruktion von Gussbauteilen revolutioniert werden kann“, sagt Felix Reissner, wissenschaftlicher Mitarbeiter im Fraunhofer LBF und Projektleiter von DNAguss. Mit seinem Team konnte er zeigen, dass die Softwarekette eine optimale Abstimmung der einzelnen Prozessschritte ermöglicht. Das Beispielbauteil, eine Welle einer Windmühle, wies sogar 34 Prozent weniger Gewicht auf. Das Team fertigte sie als Kunststoffmodell im 3D-Druck. Unterstützung bekam das Forschungsprojekt DNAguss vom Bundesministerium für Wirtschaft und Energie. Zu den weiteren Partnern zählten das Fraunhofer-Institut für Keramische Technologien und Systeme IKTS, die Hochschule für angewandte Wissenschaften Ansbach, Matplus GmbH, Magma Gießereitechnologie GmbH, Intes GmbH, HegerGuss GmbH, Meuselwitz Guss Eisengießerei GmbH, BMB Gesellschaft für Materialprüfung mbH, Magna Engineering Center Steyr GmbH & Co. KG.
Mehr zum Thema Werkstoffe:
Ein Beitrag von: