Endlich nachhaltiger Kunststoff in Sicht
US-amerikanischen Forschenden ist ein kleines Kunststück gelungen: ein neuer pflanzlicher Verbundstoff, der Zellulose-Nanokristalle in bisher nie erreichter Höhe enthält. Das könnte der Durchbruch für einen nachhaltigen Kunststoff sein.
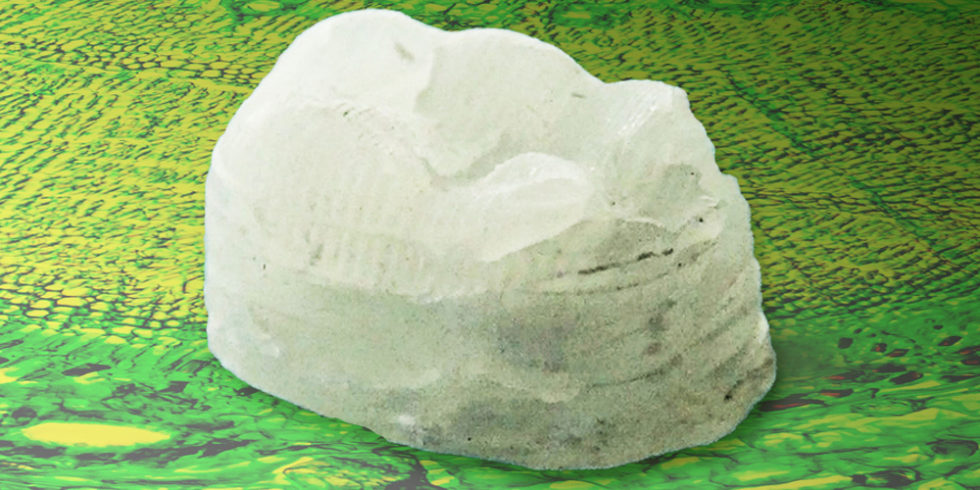
Dieser unscheinbare Klumpen könnte die Lösung sein. Es handelt sich um einen weitgehend nachhaltigen Kunststoff aus Zellulose.
Foto: MIT
Zellulosefasern sind der Hauptbestandteil aller Pflanzen, und die Industrie nutzt sie kräftig, vor allem für die Papierproduktion und für Textilien – etwa 10 Milliarden Tonnen werden jedes Jahr verarbeitet. Dieses natürliche Polymer kann aber noch viel mehr. Denn in jeder Faser stecken verstärkende Cellulose-Nanokristalle (CNCs). Dabei handelt es sich um Ketten aus organischen Polymeren, die in nahezu perfekten Kristallmustern angeordnet sind. Sie sind extrem stark und sogar fester als das synthetische Material Kevlar.
Schon lange ist klar: Wenn es gelänge, diese CNCs in größerer Menge in Werkstoffe zu integrieren, wäre ein nachhaltiger Kunststoff greifbar – der hauptsächlich aus einem natürlichen Grundstoff gewonnen würde. Genau das will ein Forschungsteam vom Massachusetts Institute for Technology (MIT) erreichen. Jetzt haben die Wissenschaftlerinnen und Wissenschaftler einen neuen Verbundstoff vorgestellt: Die organischen Kristalle haben darin einen Anteil zwischen 60% und 90%.
Leistungsfähige Kunststoffe aus der digitalen Werkstofffabrik
Einfache Lösung für eine große Herausforderung
Bisher scheiterten Forschende immer an demselben Problem, wenn sie versuchten, CNCs in größerer Menge in Werkstoffen einzubauen, um nachhaltigen Kunststoff herzustellen: Die Kristalle verklumpen relativ leicht und verbinden sich kaum mit Polymermolekülen. Die Expertinnen und Experten am MIT gingen daher einen neuen Weg. Zunächst mischten sie eine Lösung aus synthetischem Polymer mit handelsüblichem CNC-Pulver. Nach einigen Versuchen hatten sie das richtige Verhältnis von CNC zu Polymeren entwickelt, das die Lösung in ein Gel mit der richtigen Konsistenz verwandelt hat. Das heißt, sie konnten das Gel in eine Form gießen oder durch die Drüse eines 3D-Druckers pressen. Zusätzlich brachen sie die Zelluloseklumpen im Gel mit einer Ultraschallsonde auf. So erhöhten sie die Wahrscheinlichkeit dafür, dass die Zellulose starke Bindungen mit den Polymermolekülen eingeht.
Anschließend verarbeiteten die Wissenschaftlerinnen und Wissenschaftler das innovative Gel weiter. Einen Teil gossen sie in eine Form und mit einem weiteren Teil befüllten sie einen 3D-Drucker. Die gedruckten Muster ließen sie trocknen – der Werkstoff erwies sich als fester Verbundstoff, der hauptsächlich aus Zellulose-Nanokristallen besteht.
„Wir haben im Grunde genommen das Holz dekonstruiert und rekonstruiert“, sagt Abhinav Rao vom Forschungsteam. „Wir haben die besten Bestandteile von Holz, nämlich Zellulose-Nanokristalle, genommen und sie zu einem neuen Verbundwerkstoff zusammengesetzt.“
Nachhaltiger Kunststoff – unter die Lupe genommen
Als das Team die Struktur des Verbundwerkstoffs unter dem Mikroskop untersuchte, stellte es fest, dass sich die Zellulosekörner ein Zick-Zack-Muster bildeten, wie man es von der Struktur bei Perlmutt kennt. In Perlmutt verhindert diese zickzackförmige Mikrostruktur, dass ein Riss gerade durch das Material verläuft. Genau das scheint auch bei dem neuen nachhaltigen Kunststoff der Fall zu sein. Unterm Strich führt das zu einer ungewöhnlichen Härte und Steifigkeit, die nach Angaben der Forschenden an der Grenze zwischen herkömmlichen Kunststoffen und Metallen liege.
Der Verbundstoff auf natürlicher Basis ist damit stärker als einige Knochenarten und härter als typische Aluminiumlegierungen. „Indem wir Verbundwerkstoffe mit CNCs bei hoher Belastung herstellen, können wir Materialien auf Polymerbasis mechanische Eigenschaften verleihen, die sie bisher nicht hatten“, sagt John Hart, Professor für Maschinenbau. „Wenn wir einen Teil des erdölbasierten Kunststoffs durch natürlich gewonnene Zellulose ersetzen können, ist das wohl auch besser für den Planeten.“
Testweise Zahnimplantate aus nahhaltigem Kunststoff hergestellt
Die Wissenschaftlerinnen und Wissenschaftler haben den nachhaltigen Kunststoff als Praxistest sogar in die Form eines Zahns gefräst, um zu zeigen, dass das Material eines Tages für die Herstellung von Zahnimplantaten auf Zellulosebasis und weitere Kunststoffprodukte verwendet werden könnte.
Für die Zukunft sucht das Team nach Möglichkeiten, die Schrumpfung von Gelen beim Trocknen zu minimieren. Während die Schrumpfung beim Druck von kleinen Objekten kein großes Problem darstellt, könnten größere Objekte beim Trocknen des Verbundstoffs knicken oder reißen. „Wenn wir die Schrumpfung vermeiden könnten, wäre es möglich, die Herstellung des Materials vielleicht bis in den Meterbereich zu skalieren“, sagt Rao. Dann könnten synthetische Werkstoffe durch weitgehend nachhaltige Kunststoffe ersetzen werden.
Mehr Innovationen vom MIT kennenlernen:
Ein Beitrag von: