„Flüssiges“ Holz statt Plastik
Lignin als Abfallstoff der Papiererzeugung wird bisher vor allem verbrannt. Doch der Stoff mausert sich in Verbindung mit Naturfasern zu einem Material für Möbel, Schmuck und Profile.
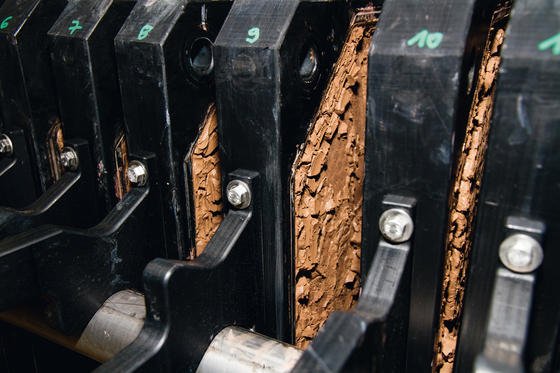
Einen ökologischen Ersatz für Erdölprodukte könnte der Holzbestandteil Lignin liefern, wie er in diese Filterpresse gewonnen wird.
Foto: Fraunhofer CBP
Ein Handy aus Holz und Hanf ? Das ist kein Witz, sondern eine umweltfreundliche Alternative zu den üblichen Kunststoffgehäusen. Denn nachwachsende Rohstoffe mausern sich zum universell einsetzbaren Kunststoffersatz. Das Fraunhofer-Institut für Chemische Technologie (ICT) in Pfinztal hat ein Verfahren zur Marktreife gebracht, aus dem Naturpolymer Lignin und aus Hanffasern eine Art flüssiges Holz herzustellen, dessen Eigenschaften denen der üblichen Kunststoffe sogar überlegen sind.
„Angefangen hat alles mit dem Hanf“, erinnert sich Helmut Nägele. Seit die Pflanze als nachwachsender Rohstoff eine Renaissance erlebt, beschäftigt sich auch Nägele mit der Idee, sie für technische Produkte zu nutzen. Denn die Faser sei im Vergleich zur Baumwolle umweltverträglicher produzierbar, zumindest unter geringerem Pestizideinsatz. Darüber hinaus sei sie sehr widerstandsfähig gegen bakterielle Zersetzung und dabei nahezu ebenso fest und leicht wie eine Glasfaser.
Dem ICT ist es gelungen, ein thermoplastisches Material zu entwickeln, das sich auf handelsüblichen Maschinen zu Formteilen mit holzähnlichem Charakter spritzen lässt. Die Wissenschaftler sprechen von „flüssig“, weil die Masse gerade so dickflüssig ist, dass sie sich noch in die Spritzgussformen drücken lässt. Zunächst werden Holzschnitzel bei hohem Druck und etwa 280 °C mit Wasser gekocht, um den etwa 30 %igen Ligninanteil von den übrigen Holzbestandteilen zu trennen. Das getrocknete Ligninpulver wird mit 1 mm bis 6 mm langen Fasern gemischt und auf 170 °C erhitzt. Es entsteht eine zähflüssige Mischung, die in die Formteile gepresst wird und aushärtet. „Wir wollen uns auf wenige Rezepturen beschränken“, erläutert Nägele. Die wichtigsten Parameter sind Faserlänge, Mengenverhältnis und die Auswahl des Fasertyps. Der Faseranteil schwankt stark und kann zwischen 20 % und 60 % liegen. Auch Flachs und Sisal sind geeignet.
Das Lignincompound bietet technische Vorteile und schont die natürlichen Ressourcen. Lignin ist nach der Zellulose das häufigste natürliche Polymer der Erde. Der Stoff, der dem Holz seine Festigkeit und Elastizität verleiht, fällt in großen Mengen als Abfallprodukt der Zellstoffproduktion an, und wird verbrannt. Nur etwa 5 % der weltweit 50 Mio. t Lignin werden bisher weiterverarbeitet, meistens als billiger Zusatz zu Spanplatten und Beton oder Futtermitteln.
„Unser Werkstoff, das Arboform, sieht fast aus wie Holz und verhält sich wie Holz“, erläutert Nägele, der gemeinsam mit dem Betriebswirt Jürgen Pfitzer in Pfinztal die Tecnaro GmbH gegründet hat. Deshalb sieht er dessen größten Vorzug in der preisgünstigen Fertigung von Trägerformteilen für futuristische Möbel, Parkettplatten und anderen optischen Oberflächen. Da der Werkstoff den gleichen Ausdehnungskoeffizienten wie Holzfurnier habe, sei er auch hervorragend als Träger für die Edelholzinterieurs von Luxuswagen geeignet. Das teure Wurzelholz werde bisher in aufwendigen und somit teuren Verfahren auf Aluminium- oder Kunststoffträger aufgeklebt.
Die ersten Produkte aus Arboform werden Uhrengehäuse und Modeschmuck sein, denn dafür sind die für den Spritzguss notwendigen Werkzeuge vorhanden. Für andere Formen müssen sie noch angepasst werden. Das Material lässt sich vor dem Spritzen einfärben, man kann es polieren oder lackieren – von der Brosche bis zum Gartenstuhl sei alles möglich. Arboform lässt sich auch extrudieren, beispielsweise für Fensterprofile. Das Material erfüllt die entsprechenden Anforderungen an den Brandschutz.
Doch so weit ist die Firma noch nicht. In der jetzt angelaufenen Startphase werden mit den Kunden die individuellen Anforderungen an den Werkstoff diskutiert. Für jedes Produkt wird zunächst nach dem optimalen Mischungsverhältnis von Fasern und Lignin gesucht. Potential zur Verbesserung der Fasereigenschaften liege auch noch in der Optimierung des Faseraufschlusses. Dennoch werde die Tecnaro noch in diesem Jahr die Produktion aufnehmen. Nägele ist sehr optimistisch, neben Uhrengehäusen und Gewehrschäften weitere Märkte zu erobern. Sein Produkt besitze eine hohe Steifigkeit und Festigkeit, es sei weitgehend CO2-neutral herstellbar und „es ist eben schön anzusehen“. UWE SCHULTE
Die beiden Fraunhofer-Forscher Nägele und Pfitzer haben das Holz neu erfunden: Der Abfallstoff Lignin, verstärkt durch Naturfasern, ergibt einen Werkstoff, der aussieht wie Holz und sich so leicht formen lässt wie ein thermoplastischer Kunststoff.
Ein Beitrag von: