Jetzt fließt auch in den USA grünes Eisen
Boston Metal hat mit einem einstufigen Verfahren erstmals Eisen ohne Belastung des Klimas produziert. Vorreiter Schweden und die deutschen Stahlwerke setzen auf einen zweistufigen Prozess
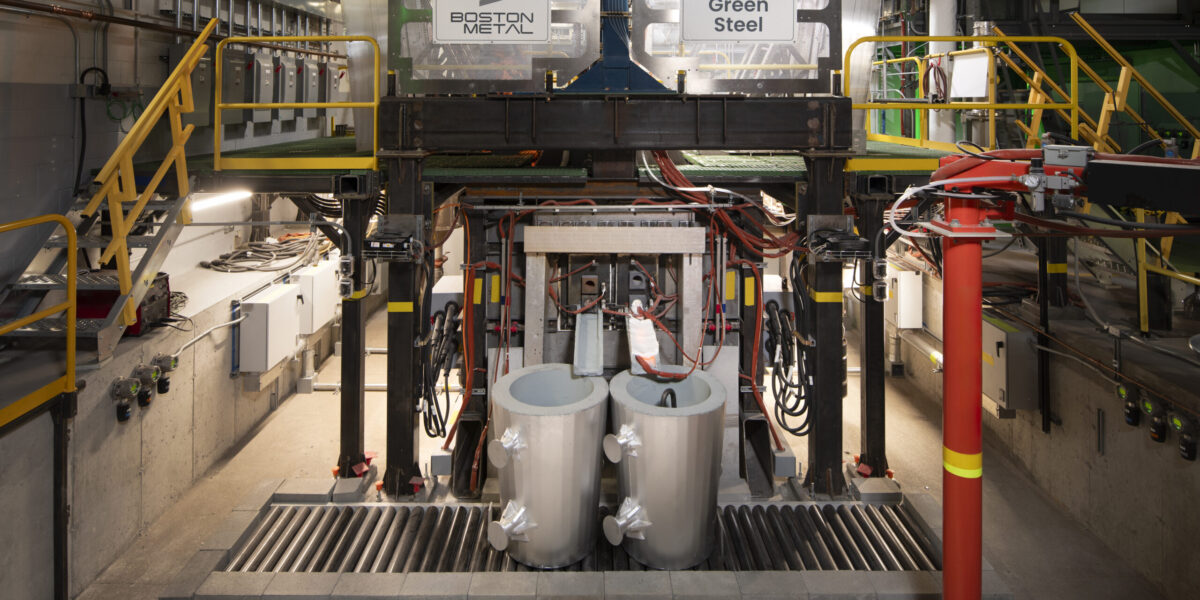
Hier stellt Boston Metal mit einem einstufigen Verfahren klimafreundliches Eisen her.
Foto: Boston Metal
Ohne auch nur eine Spur des Klimagases Kohlenstoffdioxid (CO2) zu emittieren hat Boston Metal in Woburn im US-Bundesstaat Massachusetts jetzt die erste Tonne Roheisen produziert. Während in Deutschland und in Schweden grünes Roheisen, aus dem grüner Stahl etwa für Autos, Maschinen und den Betonbau hergestellt wird, über den Umweg Eisenschwamm hergestellt wird, schaffen die Amerikaner es mit einem Verfahren, das am Massachusetts Institute of Technology (MIT) in Cambridge bei Bosten entwickelt worden ist, in einem einzigen Durchgang.
Inhaltsverzeichnis
Elektrolyse in geschmolzenem Salz
Gemeinsam ist allen Verfahren, dass sie große Mengen an grünem Strom benötigen, die Europäer für die Herstellung von Wasserstoff, die Konkurrenz jenseits des Atlantiks für die so genannte Schmelzelektrolyse. Bei diesem Prozess wird das Eisenerz in einen Mix aus heißen und deshalb flüssigen Salzen geschüttet. Dorthinein ragen Elektroden, die elektrischen Strom einleiten. Dieser erhitzt das Gemisch auf bis zu 1600 Grad Celsius.
Gleichzeitig entsteht Wasserstoff, der dem Eisenerz, das in Form von Oxid vorliegt – besser bekannt als Rost –, den Sauerstoff entzieht. Zurück bleibt Eisen in flüssiger Form, das wie beim Abstich eines klassischen Hochofens aus dem Reaktionsbehälter, der so genannten MOE-Zelle herausfließt – MOE steht für Molten Oxide Electrolysis, also Schmelzelektrolyse. Dieses Verfahren wird bisher vor allem für die Herstellung von Aluminium genutzt.
Das Produkt ist laut Boston Metal hochreines Roheisen, das direkt zu Stahl veredelt werden kann. Noch vor 2030 will das Unternehmen grünen Stahl kommerziell produzieren.
Bisher außerordentlich klimabelastend
Bisher ist die Stahlproduktion außerordentlich klimabelastend. Laut World Steel Association in der belgischen Hauptstadt Brüssel entstehen bei herkömmlicher Produktionsweise pro Tonne Stahl 1,92 Tonnen CO2. Weltweit sind das zwischen sieben und neun Prozent der weltweiten CO2-Emissionen.
Bei der Herstellung von Eisen im Hochofen wird Koks verbrannt. Dieser bezieht den Sauerstoff, den er zur Verbrennung benötigt, aus dem Eisenoxid. Bei einer Temperatur von bis zu 2000 Grad verflüssigt sich das Eisen und sammelt sich am Grund des Hochofens. Obenauf schwimmt die Schlacke, die getrennt aus dem Hochofen entfernt und beispielsweise im Straßen- oder Betonbau verwendet wird.
Direktreduktion ist am weitesten verbreitet
Ein Verfahren ohne Koks ist die Direktreduktion des Eisenerzes. Es wird dazu von den Flammen brennenden Erdgases eingehüllt, das dem Eisen den Sauerstoff entzieht Es entsteht Eisenschwamm, ein poröses Material, das neben Eisen auch Mineralien enthält. Beide Fraktionen werden durch Verflüssigen getrennt.
Europa setzt auf Direktreduktion
Erdgas, das bei diesem Verfahren bei weitem dominiert, lässt sich durch Wasserstoff ersetzen, der in einer Elektrolyseanlage hergestellt wird. Die Energie liefert grüner Strom. ThyssenKrupp in Duisburg, ArcelorMittal in Hamburg, der Stahlkonzern Salzgitter, Saarstahl in Dillingen und der schwedische Konzern SSAB setzen auf dieses Verfahren. ThyssenKrupp hat es bereits in einer Pilotanlage erprobt, SSAB sogar den ersten Stahl, der aus grünem Roheisen hergestellt worden ist, an den Autohersteller Volvo geliefert.
Die Schweden haben die Nase vorn
All diese Hersteller bauen oder planen derartige Anlagen, die Wasserstoff aus betriebseigenen Elektrolyseuren beziehen werden. SSAB will bereits 2026 grünen Stahl in großen Mengen herstellen. Salzgitter und ArcelorMittal wollen schon in diesem Jahr einen Teil des Erdgases durch Wasserstoff ersetzen. Saarstahl plant den 100-Prozent-Einsatz von Wasserstoff für 2027/28.
Eisenschwamm wird direkt veredelt
Thyssenkrupp Steel, das 2029 in seiner Direktreduktionsanlage in Duisburg Erdgas komplett durch Wasserstoff ersetzen will, geht bei seinem Projekt einen neuen Weg. Der rund 500 Grad Celsius heiße Eisenschwamm aus der mit Wasserstoff betriebenen Direktreduktionsanlage soll unter Ausnutzung der Hitze in einem nachgelagerten Einschmelzer verflüssigt werden, sodass es direkt wie zuvor das Hochofen-Roheisen im Konverter des Stahlwerks unter Zugabe von Schrott und Zuschlagstoffen zu Stahl veredelt werden kann.
Lesen Sie dazu auf vdi-nachrichten.com: So funktioniert Direktreduktion
Ein Beitrag von: