„Machen, statt Bedenken tragen!“
Küchensiebe wurden lange Zeit bei Gebrüder Kufferath in Düren (GKD) produziert. Das ist aber nun Vergangenheit, wie Vorstand Ingo Kufferath den VDI nachrichten verdeutlichte. Heute entwickelt das Unternehmen Sieb- und Filtermedien, Prozessbänder und Gewebe für die Architektur nach Kundenwunsch.
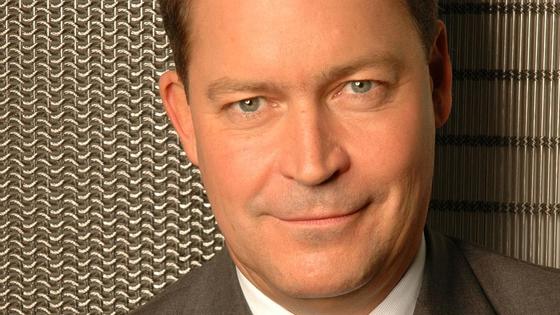
Ingo Kufferath: "Ich bin ständig auf dem Trip, Neues zu entdecken."
Foto: GKD
Ob Filtermedium im Tintenstrahldrucker, Stützgewebe im Airbag, Ölfilter, Wundpflaster oder Windel: „Sie glauben nicht, wie viele Produkte des täglichen Lebens mit GKD in Verbindung kommen“, sagt Ingo Kufferath, Vorstand der GKD – Gebr. Kufferath in Düren. Zusammen mit seinem Bruder Stephan steht der 53-Jährige in dritter Generation an der Spitze eines Familienunternehmens, das sich in kaum zwei Jahrzehnten von der Metallweberei zum weltweiten „Anbieter gewebebasierter Lösungen“ weiterentwickelt hat. „Ich stehe im Haus für die Innovationskultur“, sagt Kufferath stolz. „Ich bin ständig auf dem Trip, Neues zu entdecken.“
Kufferath war 26 und hatte gerade sein Maschinenbaustudium abgeschlossen, als sein Vater das Unternehmen aus Altersgründen an die Söhne übergeben wollte. Mit 29 wurde er bereits Geschäftsführer und ist nach Umwandlung der GKD in eine AG seit 2001 Vorstand. „Auch wenn es das Unternehmen nicht gegeben hätte“, so der drahtige Manager, „ich wäre Ingenieur geworden.“
Kufferath versteht nicht nur viel von Maschinen. In den 90er-Jahren hat er die Fraktalisierung der Geschäftsprozesse durchgesetzt. „Wir haben unser Unternehmen komplett umgebaut, mit allem, was dazu gehört“, erinnert sich Kufferath. Herausgekommen sei eine stringente Prozessorganisation und eine stärkere Marktausrichtung. Damals formierten sich die drei heute unabhängig agierenden Geschäftsbereiche Solid Weave, Weave in Motion und Creative Weave.
Solid Weave entwickelt Sieb- und Filtermedien für Schlüsselindustrien wie Automobil-, Luft- und Raumfahrtindustrie und die Umwelttechnik. Weave in Motion fertigt Prozessbänder für industrielle Anwendungen, z. B. in der Lebensmittel-, Vliesstoff- und Holzindustrie. Creative Weave ist der Spezialist für Architektur- und Designgewebe.
Kufferath ist überzeugt: „In der Breite der Anwendungen gibt es weltweit keinen Hersteller, der mit GKD direkt vergleichbar ist.“ Viel innovatives Potenzial liege heute in neuen Werkstoffen, sagt Kufferath. „Wir haben keine Berührungsängste und beschäftigen uns z. B. mit Fasern, Garnen, mit Bambus und Glas.“ Gerade sei ein Projekt angelaufen, bei dem Fasergarn aus Basalt mit Edelstahl zu einem hybriden Filter gewebt wird. Der mineralische Werkstoff Basalt sei dabei widerstandsfähig gegen aggressive Chemikalien und hohe Temperaturen.
GKD habe in der Gewebeentwicklung schon viele Standards gesetzt. Grundsätzlich arbeite man daran, Produkte kundenbezogen zu veredeln und mit immer mehr Merkmalen zu versehen, „damit der Kunde von uns ein fertiges Produkt bekommt, welches er einfach in seine Anlage einbauen kann.“
Dank WeaveGeo, einer Simulationssoftware zur Entwicklung von ein- und mehrlagigen Gewebestrukturen, die GKD zusammen mit dem Fraunhofer Institut für Techno- und Wirtschaftsmathematik (ITWM) in Kaiserslautern ständig weiterentwickelt, könne GKD innovativere Lösungen anbieten. Durch die Simulation habe das Unternehmen zudem sein Wissen über Filtrationsprozesse erheblich erweitert und Kompetenzen für die Konstruktion und den Bau von Filteranlagen aufgebaut. Seit 2007 bietet GKD das Kompaktfiltersystem Maxflow zur Filtration von Kühlschmiermitteln in der metallverarbeitenden Industrie an, welches die Filtration und Brikettierung in einer Anlage erlaube.
Die Offenheit für Neues, auch der Spaß daran, und die Bereitschaft, über klassische Produkte und Herstellungsmethoden hinauszugehen, sei ein Kennzeichen des Unternehmens: „Unsere einzige Konstante ist der stetige Wandel.“ Zu dieser Offenheit gehöre es auch, Produkte auf den Prüfstand zu stellen. „Vor zehn Jahren haben wir in großen Mengen Küchensiebe gefertigt“, so Kufferath. Heute rechne sich das wegen der Konkurrenz aus China nicht mehr. „Wenn nötig, werfen wir Produkte über Bord“, sagt der GKD-Chef bestimmt. „Deshalb erleiden wir nicht das Schicksal der Textilindustrie.“
Eine gewisse Nähe zur Textilindustrie zeigen die Produktionsmittel bei GKD dennoch. Lieferanten aus Deutschland und Italien bauen die Maschinen, häufig Textilmaschinenderivate, die „wir mit Tricks und eigenem Engineering weiterentwickeln oder umbauen, je nachdem, welches Material wir verweben wollen.“ So erinnere manches im Unternehmen an den Textilbereich, sei aber „letztlich doch ganz anders.“ Zwischen 5 % und 10 % des Umsatzes investiere GKD in die Produktion. „Wir wollen technologische Standards setzen und noch präziser und nachhaltiger produzieren.“ Teile der Produktion, wie der Mikrofilterbereich, sind hochautomatisiert, in bestimmten Bereichen sichere aber nur Handarbeit die erforderliche Qualität.
„Dass wir unsere technischen Produkte auch für ganz andere Anwendungen einsetzen können“, entdeckten die Gebrüder Kufferath, als Dominique Perrault 1992 an ihre Tür klopfte. Der französische Architekt suchte für die Fassadengestaltung der neuen Nationalbibliothek in Paris einen ganz besonderen Schmuck: breite, schöne Metallgewebe aus Seilen und Drähten. „Die Eintrittsschwelle war maschinell gesehen nicht groß“, urteilt Kufferath heute. Aber der Fertigungsprozess sei eine gewaltige Umstellung gewesen. „Wir dachten in Maschenweiten, Öffnungen und Filterfluss, aber nicht in einer Oberflächenstruktur in nicht genormten Maßen, die aus 10 m Entfernung schön aussieht“.
Getragen von der Begeisterung, Neuland zu erobern und getreu dem Motto „Machen, statt Bedenken tragen!“, stürzte sich GKD ins Projekt, fertigte monatelang Muster und entwickelte eine völlig neue Produktpalette, die passte. Was GKD heute in dieser Sparte anbiete, gehe weit über ästhetische Ansprüche hinaus. Die Gewebesysteme erfüllten z. B. klimatechnische oder akustische Funktionen. „Unser neues Highlight: Wir bringen Leuchtdioden ins Gewebe, um dem Kunden bildhaften Inhalt anzubieten.“ Als bisher größter Auftrag für das Unternehmen werde derzeit eine transparente Medienfassade für den Flughafen Doha in Katar als Komplettlösung mit zugehörender Ansteurung realisiert.
Bei aller prozessbezogenen Fraktalisierung der Geschäftsbereiche sei es heute eine große Herausforderung, „den Unternehmensverbund zusammenzuhalten“, sagt Kufferath. „Vernetzung ist die Aufgabe, die derzeit einen Großteil meiner Zeit und der meines Bruders im Unternehmen ausmacht.“ Gerade auch für Innovationen sei es wichtig, dass es einen kontinuierlichen Informationsfluss gebe und sämtliche Lösungsansätze in einer Art Systembaukasten zusammengeführt würden. Dafür gibt es bei GKD regelmäßige Treffen.
Knapp 400 der rund 600 Mitarbeiter von GKD arbeiten heute am Stammsitz in Düren. Zudem gibt es Tochtergesellschaften in China sowie in Südafrika. Der Standort Düren sei aber nicht in Frage gestellt. Kufferath hat gute Gründe: „Unsere Mitarbeiter haben hier fast alle ihre Wurzeln und wir fast keine Fluktuation.“
Auch zukünftig werde sich das Unternehmen ständig verändern, um am Markt erfolgreich zu bleiben. Bei allem Wandel gebe es aber durchaus Beständigkeit: „Wir haben die Gewinne stets überwiegend reinvestiert und das wissen die Mitarbeiter auch zu schätzen.“ HEIKE FREIMANN
Ein Beitrag von: