MAX-Phasen schützen Flugzeugturbinen vor Sand
Einem extrem festen, hitzebeständigen und gut formbaren Material könnte die Zukunft gehören. Bisher ließ es sich nur mit hohem Aufwand und hohen Kosten herstellen. Jetzt gab es den ersehnten Durchbruch.
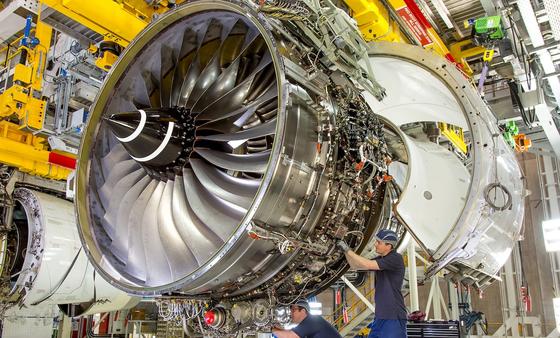
Produktion einer Flugzeugturbine bei Rolls-Royce: Die Ingenieure streben eine saubere Verbrennung an. Denn dann sinken Treibstoffverbrauch und Emission.
Foto: Rolls-Royce
Max-Phasen gelten als Material der Zukunft. Es ist leicht, temperaturbeständig und hart wie Keramik, dabei aber gut formbar wie Metalle, die erwärmt sind. Sie gelten als idealer Werkstoff für hoch belastete Turbinen in Kraftwerken und Flugzeugen, Raumfahrtanwendungen oder medizinische Implantate wie künstliche Hüftgelenke. Doch die Herstellung gelang bisher nur in kleinen Mengen im Labor.
Ein Salzmantel verhindert unerwünschtes Oxidieren
Wissenschaftler am Forschungszentrum Jülich (FZJ) haben jetzt einen Weg gefunden, MAX-Phasen-Pulver in großen Mengen herzustellen, ein Verfahren, das auch die Industrie nutzen könnte. Das Problem: Das Ausgangsmaterial, das unter anderem ein Metall wie Titan enthält, muss auf mehr als 1000 Grad Celsius erhitzt werden. Dabei oxidiert es und macht es unbrauchbar.
Apurv Dash, Doktorand am FZJ, fand die Lösung, weil ihm kein Vakkuumofen zur Verfügung stand, der üblicherweise benutzt wird, um Oxidation zu vermeiden. Er experimentierte mit einem normalen Ofen. Um dennoch das Oxidieren auszuschließen schloss er den Klumpen Ausgangsmaterial in Kaliumbromid ein, ein Salz, das schon vor dem Schmelzen des Salzes bei 735 Grad Celsius den Sauerstoffkontakt zu unterbindet, ein Salzmantel als Schutzschild. Oberhalb dieser Temperatur verflüssigt es sich, bleibt aber weiterhin eine luftdichte Hülle.
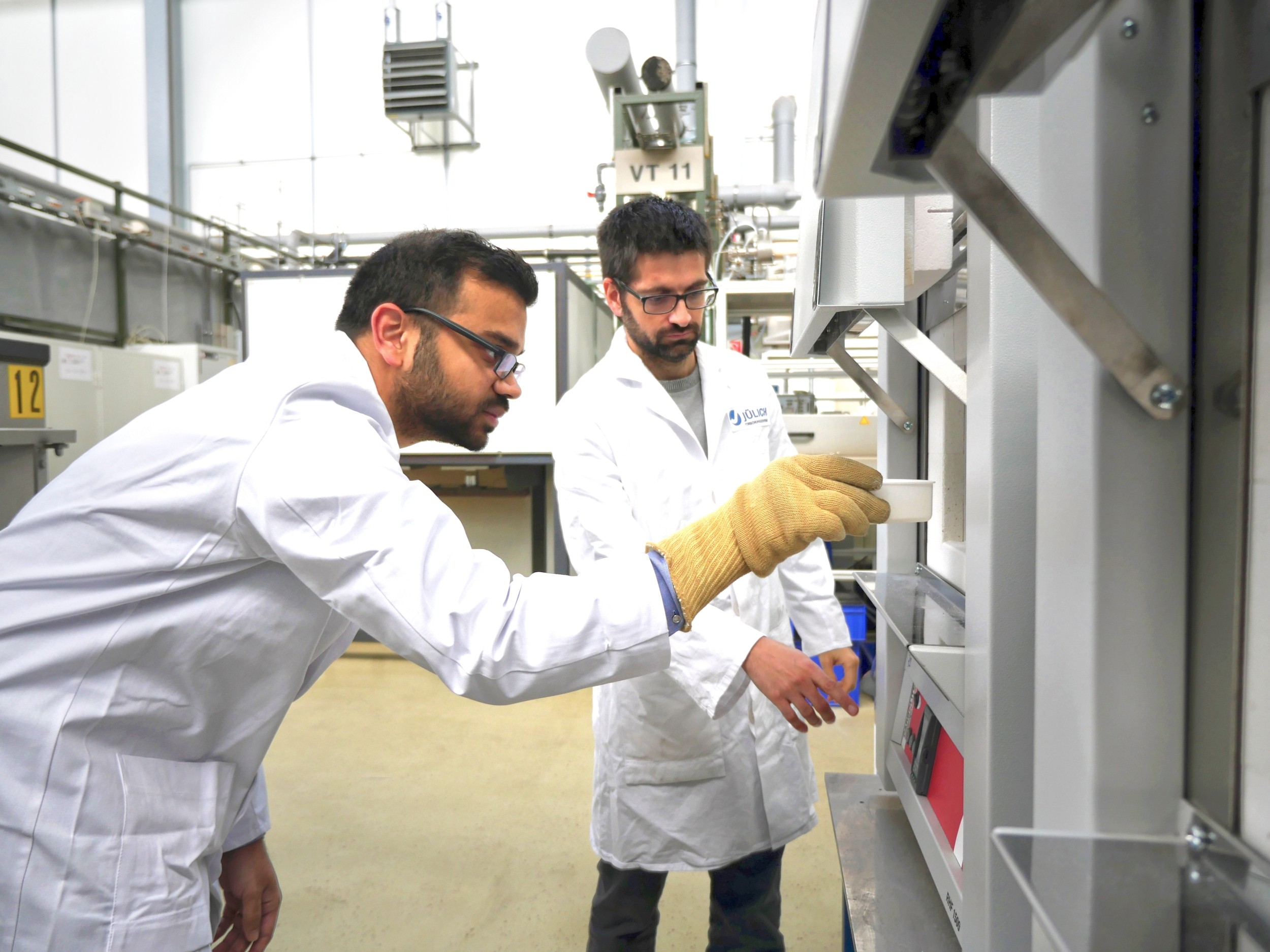
Mit dem neuen Verfahren reicht nun schon ein normaler Ofen. Im Bild: Dr. Jesus Gonzalez-Julian (rechts) und Apurv Dash (links)
Foto: Forschungszentrum Jülich / Regine Panknin
Energieaufwändiger Mahlvorgang entfällt
Das Salz wirkt außerdem als Trennmittel. Es bilden sich MAX-Phasen-Körnchen, die nicht aneinanderbacken und anschließend mit relativ hohem Energieaufwand gemahlen werden müssen. Wenn das Salz abgewaschen wird, bleibt pulverförmiges Material übrig, das sich zu Bauteilen formen lässt. Das Salz hat noch einen weiteren erfreulichen Nebeneffekt. Die Ausgangsmaterialien verbinden sich schon bei niedrigeren Temperaturen als im Vakuumofen. Das spart noch einmal Energie. „In der industriellen Produktion spielen MAX-Phasen daher bislang praktisch keine Rolle“, sagt Junior-Professor Jesus Gonzalez-Julian, Nachwuchsgruppenleiter am FZJ. Das dürfte sich jetzt ändern.
Verfahren mit geschmolzenem Salz werden bereits seit längerem zur Herstellung von Pulvern aus nicht-oxidischen Keramiken genutzt. Dazu zählen Nitride, Karbide und Boride. Das funktioniert nur in einer Schutzgasatmosphäre. Dazu kann man beispielsweise das Edelgas -Argon nehmen. Das verteuert die Herstellung. Mit Kaliumbromid könnte auch bei dieser Produktionstechnik auf das Schutzgas verzichtet werden.
MAX-Phasen-Material enthält ein Metall, ein Element aus den Alkali- oder Erdalkalimetallen sowie Kohlenstoff oder Stickstoff. Die Bestandteile sind Kristallin und in Lagen übereinander angeordnet. Das verleiht dem Material seine ungewöhnlichen Eigenarten.
Luftfahrt: Vulkanasche verliert ihren Schrecken
Es ist wahrscheinlich zu teuer, ganze Bauteile aus diesem Material zu formen. Es lässt sich allerdings auch nutzen, um weniger edle Werkstoffe zu beschichten und ihnen damit bessere Eigenschaften zu geben. Flugzeugturbinen beispielsweise. Viele stark frequentierte Flughäfen befinden sich in sandreichen Regionen. Bei starkem Wind befinden sich einzelne Sandkörnchen in der Luft, die die Turbinen ansaugen. Diese lassen die Schaufeln erodieren. Ebenso Asche aus Vulkanen, die die Luftfahrt im Extremfall lahmlegt wie 2015 nach dem Ausbruch des isländischen Vulkans Eyjafjallajökull. MAX-Phasen-Beschichtungen können diese Erosion verhindern.
Im gerade gegründeten Christian-Doppler-Institut für Beschichtungstechnik in Wien dürfte das Herstellungsverfahren des Pulvers von höchstem Interesse sein. Denn verschleißfeste Schichten zu entwickeln ist die Kernaufgabe des Instituts.
Ein Beitrag von: