Neue Schweißverfahren für den Hochleistungsstahl T24
Der Hochleistungsstahl T24 hat hohes Potenzial, wenn es darum geht, den aktuellen Forderungen nach mehr Energieeffizienz gerecht zu werden. Allerdings machten immer wieder Risse in den Schweißnähten Probleme. Neue Verarbeitungstechniken scheinen das Problem zu lösen.
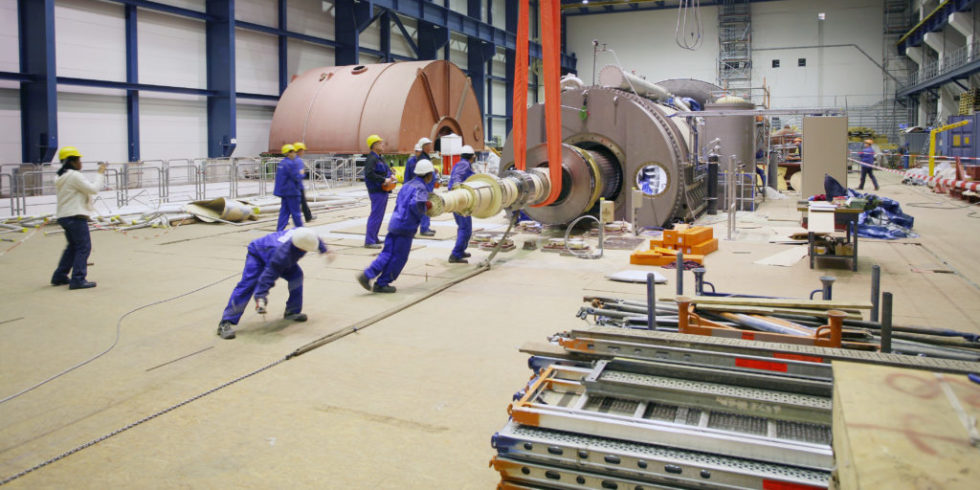
Der Hochleistungsstahl T24, der beispielsweise im Vattenfall-Kraftwerk in Boxberg in der Lausitz eingesetzt wurde, hat immer wieder Probleme mit den Schweißnähten. Jetzt wurden Schweißverfahren entwickelt, die das Problem lösen. (Symbolfoto)
Foto: Vattenfall/Bernd Schnabel
Insbesondere Steinkohle- und Braunkohlekraftwerke sehen sich mit den Forderungen nach höheren Wirkungsgraden und deutlich niedrigeren CO2-Emissionen konfrontiert. Das macht den Einsatz neuer Werkstoffe im Bereich der Dampferzeugung, der Dampfleitungen und der Dampfturbine notwendig.
Mit dem Anfang der 90er-Jahre entwickelten Werkstoff 7CrMoVTiB10–10, auch T24 genannt, schien das Problem gelöst zu sein. Das Material ermöglicht einen signifikant verbesserten Anlagenwirkungsgrad. Gleichzeitig lässt sich der spezifische CO2-Ausstoß reduzieren. Das Problem war nur, dass während der Inbetriebnahme neu gebauter Kessel vor allem im Verdampferteil Risse in den T24-Schweißnähten auftraten. Ausgelöst werden sie durch Spannungskorrosion.
So hatten zum Beispiel der Energiekonzern Vattenfall im Kraftwerk Boxberg beim Block R und der Essener Energieerzeuger Steag in Duisburg-Walsum im Steinkohlekraftwerksblock 10 mit entsprechenden Schwierigkeiten zu kämpfen. Intensive Diskussionen zwischen Betreibern, Herstellern und Forschungseinrichtungen sowie Versuche unter Baustellenbedingungen führten schließlich zur Modifizierung der chemischen Zusammensetzung.
Fabian Stahl: Man darf den Respekt vor martensitischen Stählen nicht verlieren
Die Experten stellten mithilfe von Testläufen fest, dass sich beim Schweißen von T24-Rundnähten ein hoher Martensitanteil sowohl in der Wärmeeinflusszone (WEZ) als auch beim Schweißgut einstellt. Ein Sachverhalt, der sich auch dann nicht verbessert, wenn bei maximal zulässiger Vorwärmtemperatur von 100 °C bis 150 °C bzw. einer Zwischenlagentemperatur von <250 °C geschweißt wird. Im Gegenteil, der größere Wärmeeintrag wirkt sich eher negativ aus, wobei dünnwandige Rohre grundsätzlich am ehesten überhitzen.
Um die Martensitbildung und die damit verbundene Aushärtung einzuschränken, wurde der Kohlenstoffgehalt im Rohr auf maximal 0,10 % begrenzt. Darüber hinaus binden zulegierte Elemente wie Vanadium und Titan den Kohlenstoff als Sonderkarbide ab. Dadurch verringern sich sowohl die mechanischen Spannungen als auch der Kohlenstoffgehalt.
Neben der spannungsarmen Herstellung ist die fachgerechte Verarbeitung der Rohrwände extrem wichtig. „Man muss keine Angst vor martensitischen Stählen haben, aber man darf den Respekt nicht verlieren“, sagt Fabian Stahl, Leiter Forschung und Entwicklung Bilfinger Piping Technologies.
Permanente Schweißaufsicht ist notwendig
„Damit die Schweißer bei der Verarbeitung auf die spezifischen Anforderungen von T24 eingehen können, müssen sie die Charakteristika verstehen. Schulungen und kontinuierliche Unterweisungen bilden dafür einen wichtigen Qualitätsbaustein. Die Trainings halten die Schweißexperten über die speziellen Vorgaben auf dem Laufenden“, ist Stahl überzeugt. Hinzu kommt die Notwendigkeit einer permanenten Schweißaufsicht. Sie erfasst und bewertet den Zustand der Anlage durch konsequente Analyse ausgewählter Bauteile und Systeme.
Mit der erstmals 2009 veröffentlichten Richtlinie VGB-Standard-S-506 zeigt der europäische technische Fachverband VGB unterschiedliche Methoden zur Zustandsbewertung und Überwachung auf. Bausteine wie Beschreibung, Dokumentation und Diagnose des Istzustands aller Komponenten und Leitungen bilden dabei die Grundlage. Zu berücksichtigen sind danach außerdem spezifische Faktoren und unvermeidbare Zusatzbeanspruchungen.
Für ältere Anlagen, für die eine Dokumentation der Anlagenhistorie über einen Zeitraum von etwa zwölf Jahren vorliegt, eignet sich beispielsweise die statistische Methode. Mit dem Verfahren lassen sich besonders Komponenten überprüfen, die hohen Drücken ausgesetzt sind. Betriebs- und Prozessdaten, die die Qualität aus Herstellung, Montage und Instandhaltung aufzeigen, ermöglichen eine strukturierte Einschätzung der Schadensanfälligkeit. Auch lassen sich Schadensursachen ableiten.
Verschiedene Techniken zur Analyse möglicher Schäden
Dagegen setzen probabilistische Methoden auf die Vorhersage von Schäden. Im Unterschied zum statistischen Verfahren greift dieser Ansatz auf Modelle zurück. Voraussetzung hierfür ist eine vollständige Datenbasis. Zwei Konzepte bieten sich an: einmal die RCM genannte zuverlässigkeitsorientierte Methode (Reliability-Centred-Maintenance), die vorzugsweise bei rotierenden Bauteilen oder leittechnischen Einrichtungen zum Einsatz kommt. Dagegen wird die RBI/RBM genannte risikobasierte Methode (Risk-Based Inspection/Risk-Based Maintenance) eher bei statischen Bauteilen angewandt. Hier liegt der Schwerpunkt auf altersbedingten Schädigungen wie Korrosion.
Die Analyse der Ausfallwahrscheinlichkeit erfolgt bei beiden Ansätzen über die Abschätzung einzelner Systeme und Komponenten. Stehen die risikorelevanten Faktoren fest, wird die Datenbank entsprechend ergänzt. Nach einer detaillierten Zusammenfassung lassen sich mithilfe einer Matrix Parameter wie Zuverlässigkeit, Eintrittswahrscheinlichkeit eines Schadensfalles, Gefährdungspotenzial und Verfügbarkeit bewerten.
Eine weitere Herangehensweise ist die detaillierte inelastische Analyse. Jedoch ist hier die Praxistauglichkeit bislang noch nicht nachgewiesen. Denkbar ist aber, die Lebensdauer zukünftig auf Basis von analytischen Zusammenhängen rechnerisch darzustellen. Mithilfe genauer Ermittlung lokaler Spannungen und Dehnungen wird die Gefahr möglicher Schäden bewertet. Die Ergebnisse dienen dann als Grundlage für die Planung regelmäßiger Prüfungen.
Ein Beitrag von: