Neues Schmiedeverfahren reduziert Materialverlust deutlich
Kurbelwellen können künftig mit deutlich weniger Stahl und Energie hergestellt werden: Dank eines neuen Verfahrens ist ein Drittel weniger Stahl notwendig, der Energiebedarf sinkt um ein Fünftel. Nach Angaben der Entwickler ist die mehrdirektionale Schmiedetechnik nur noch einen kleinen Schritt von der Anwendungsreife entfernt.
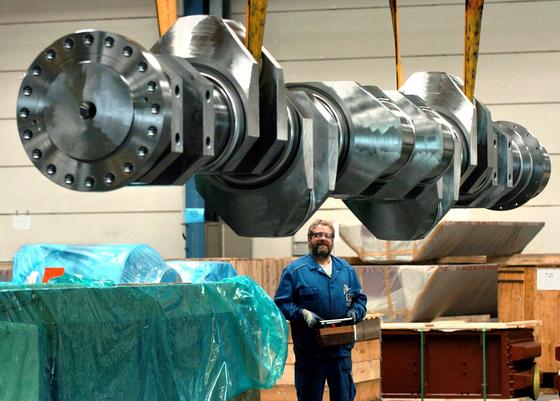
Eine bei Caterpillar Motoren in Warnemünde hergestellte Kurbelwelle für die Montage in einem Schiffsmotor: Ingenieure des IPH Hannover haben jetzt eine Schmiedetechnik entwickelt, die deutlich weniger Stahl und Energie bei der Herstellung von Kurbelwellen verbraucht.
Foto: Bernd Wüstneck/dpa
Beim Schmieden von Kurbelwellen und anderen Maschinenbauteilen beträgt der Gratanteil, der abgefräst werden muss, oft mehr als die Hälfte des Materials. Mit ihrem neuen Verfahren konnten Forscher am Institut für Integrierte Produktion Hannover (IPH) die Abfallmenge bei der Herstellung einer Kurbelwelle auf sieben Prozent senken. Möglich wird dieser große Sprung durch eine Schmiedetechnik, die mehrdirektional funktioniert, also das Werkstück von mehreren Seiten bearbeitet.
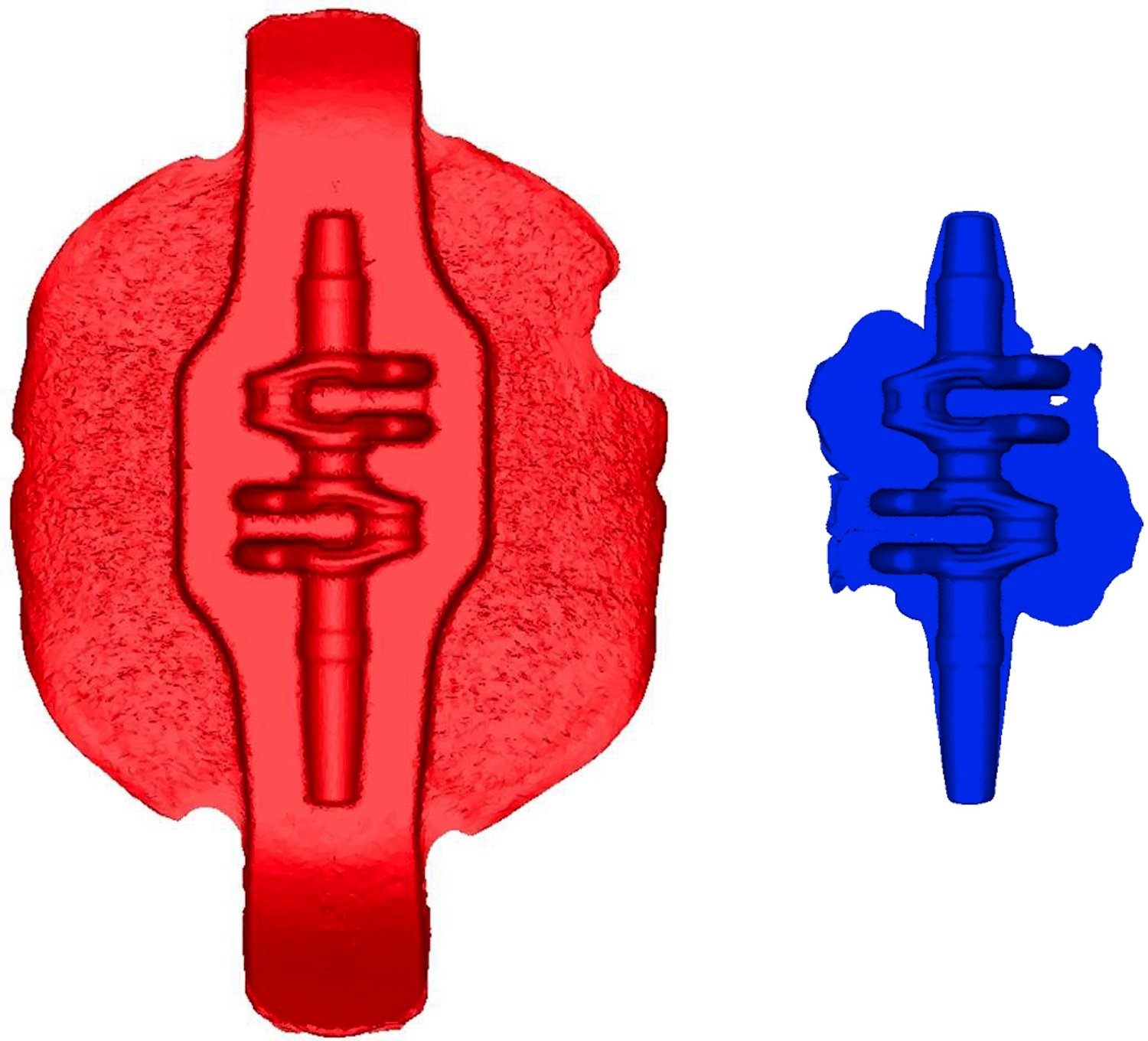
Der Unterschied beim Gratanteil ist deutlich zu sehen: Die gleiche Kurbelwelle nach dem herkömmlichen (l.) und dem mehrdirektionalen Schmiedeverfahren.
Quelle: IPH
Beim herkömmlichen Verfahren wird der erhitzte Stahl nur durch Druck von oben geformt. Dabei entweicht überschüssiges Material zur Seite. Bei der neuen Methode werde auch seitlicher Druck ausgeübt. Dadurch entstehe viel weniger „Grat“, sagen die Forscher.
Kurbelwellen für Schneemobile
Den Praxistest habe die Entwicklung bereits bestanden, erklärt das Institut: Für die Produktion einer Zweizylinderkurbelwelle seien statt 10,8 nur noch 7,5 Kilogramm Stahl notwendig. Außerdem spare das Verfahren auch noch 20 Prozent Energie, weil das Metall weniger erhitzt werden müsse.
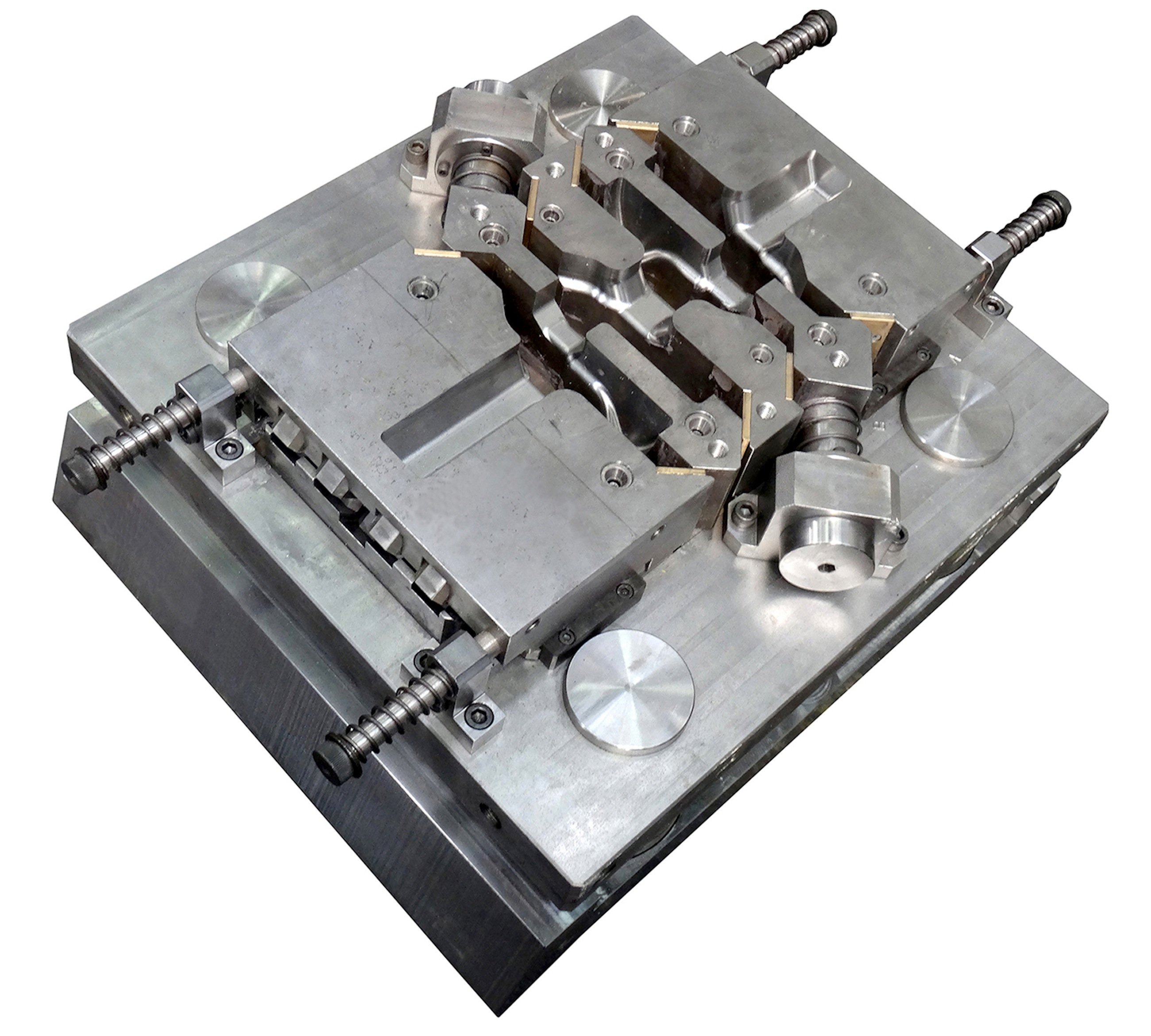
Das Schmiedewerkzeug kann in eine herkömmliche Industriepresse eingesetzt werden.
Quelle: IPH
Ein Partnerunternehmen in der Türkei habe auf diese Weise bereits Prototypen von Kurbelwellen für Schneemobile und Quads hergestellt. Jetzt soll die Technik auch bei anderen Typen von Kurbelwellen angewendet werden. „Bis zur Anwendungsreife ist es also nur noch ein kleiner Schritt“, heißt es beim IPH. Und der potenzielle Absatzmarkt ist riesig, schon allein in der Autoindustrie. Ein Beispiel: ThyssenKrupp betreibt seit 2012 in China ein Werk mit einer einzigen Hochleistungspresse, in der pro Tag bis zu 1000 Kurbelwellen produziert werden – und das nur für chinesische Nutzfahrzeuge.
Industrie kann Kosten sparen
Die Methode, die auf mehr als zehnjähriger Forschungsarbeit beruht, könnte angesichts steigender Energiepreise und hohen Kostendrucks gerade in der Metallindustrie für viele Unternehmen interessant sein. Besonders bei komplexen Bauteilen für Maschinen ist Effizienz in der Herstellung bei stabiler Qualität gefragt – gerade im Hinblick auf die Konkurrenz in Asien.
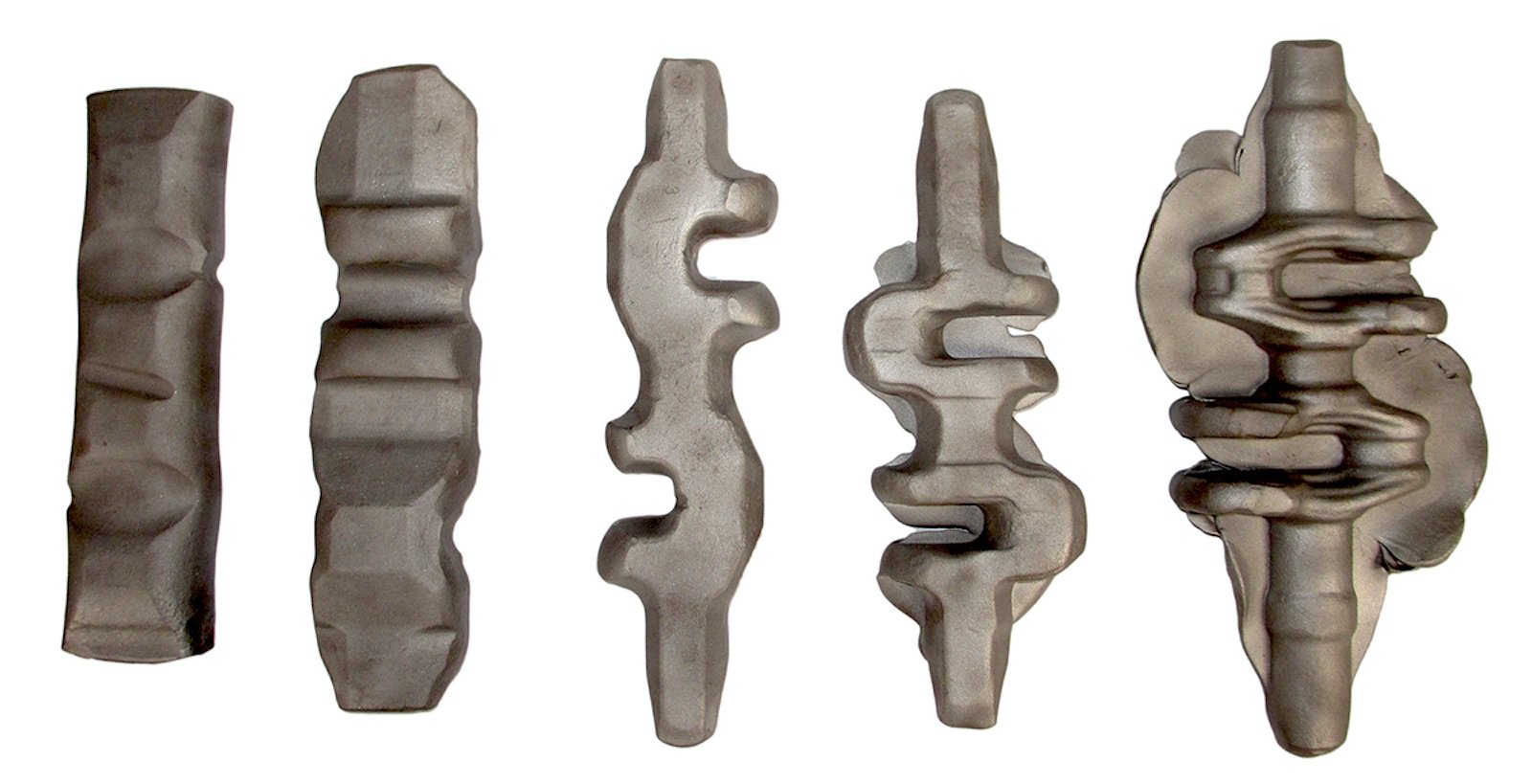
Fünf Schmiedeschritte sind bis zur fertigen Kurbelwelle nötig.
Quelle: IPH
Deshalb hat die EU das Forschungsvorhaben, an dem insgesamt sechs Unternehmen und Institute in vier Ländern beteiligt sind, mit rund 1,1 Millionen Euro gefördert. Das Institut für Elektroprozesstechnik der Leibniz-Universität Hannover hat sich in dem Projekt mit der Auslegung der Erwärmungsprozesse und der Energiebilanz des Schmiedeverfahrens beschäftigt. Das IPH selbst ist eine Ausgründung der Leibniz-Universität.
Ein wichtiger Vorteil dürfte sein, dass keine komplett neue Maschine notwendig ist, um das Verfahren anzuwenden. Das von einer spanischen Firma produzierte Umformwerkzeug kann nach Angaben des IPH in eine „ganz normale“ Exzenterpresse eingesetzt werden. Dort leitet es den Pressendruck so um, dass der Stahl gleichzeitig von oben und von den Seiten geformt wird.
Ein Beitrag von: