Stahl mit regelmäßigen Kristallgittern rostet schneller
Stahl mit geordneten Kristallgittern und ungleichmäßig verteilten Atomen rostet leichter. Diese Erkenntnis könnte Materialwissenschaftlern künftig bei der Herstellung von Stahl helfen, der besser gegen Rost geschützt ist.

Stahl mit ungeordneten Kristallgittern kann sich besser gegen Korrosion schützen. Solche amorphen Stähle entstehen bei niedrigeren Temperaturen.
Foto: ThyssenKrupp
Ein Forscherteam des Max-Planck-Instituts für Eisenforschung in Düsseldorf hat die Mikro- und Nanostruktur einer amorphen Stahllegierung aus Eisen, Chrom, Molybdän, Bor und Kohlenstoff (Fe50Cr15Mo14C15B6) untersucht und dabei herausgefunden, dass auch Gitterstruktur und Anordnung der Atome großen Einfluss auf das Rostverhalten des Stahls besitzen. „Unsere Erkenntnisse erklären, warum manche Materialien besonders anfällig für Korrosion sind, obwohl sie genauso zusammengesetzt sind wie korrosionsbeständige Stähle“, sagt Frank Renner, der die Studie am Max-Planck-Institut für Eisenforschung leitete.
Rostanfälligkeit trotz gleicher Zusammensetzung unterschiedlich
Die Forscher entwickelten eine Test-Legierung, die den gängigen Chrom-Molybdän-Stählen ähnlich ist. Der einzige Unterschied lag in dem höheren Anteil an Kohlenstoff und Bor. Jedoch war es nur mit dieser Mixtur möglich, eine amorphe Variante der Legierung zu mischen. „Für uns ist die Legierung vor allem als Modellsystem interessant, in dem wir den Übergang von der amorphen zur kristallinen Form studieren können“, so Renner.
Die Düsseldorfer Forscher stellten fest, dass Stahl eher rostet, wenn seine Struktur geordneter ist und seine Atome ungleichmäßiger verteilt sind. Besitzt die Legierung kein regelmäßiges Kristallgitter, bildet sich auf der Oberfläche eine passivierende Schicht, die das Material vor Sauerstoff schützt und so Korrosion reduziert. Außerdem hängt es nicht nur von der Zusammensetzung der Komponenten ab, wie weit die Materialien rosten. Auch die Materialverarbeitung und die Temperatur des Einsatzes sind entscheidend.
Atome gruppieren sich mit steigender Temperatur um
Auf die Spur ihrer Entdeckung kamen die Forscher, weil sie ihre Legierung verschiedenen Temperaturen aussetzten und dann jeweils das Rostverhalten mit der Gitter- und Atomstruktur verglichen. Zunächst untersuchten sie die amorphe Form der Legierung, die bei 550 Grad entsteht. Bei 800 Grad entstand die vollkommen kristalline Form, Zwischenstufen entwickelten sich zwischen 620 und 670 Grad Celsius.
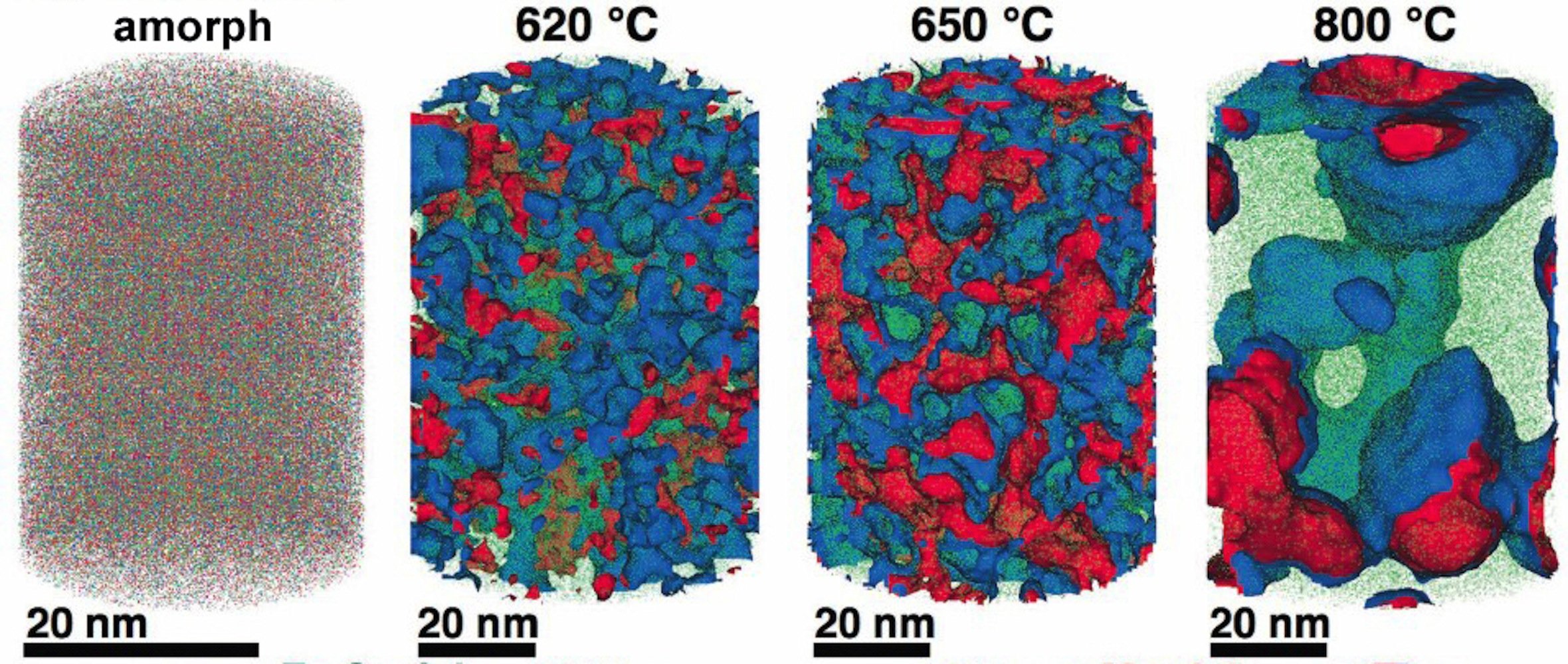
Die Nanostruktur von Stahl ist entscheidend für seine Korrosionsbeständigkeit: Die Verteilung von Eisen (grün), Chrom (blau), Molybdän (rot), Kohlenstoff und Bor hängt von der Temperatur ab, der sie zuvor ausgesetzt war. In amorphem Stahl (l.) mit ungeordneter Struktur sind die Elemente gleichmäßig verteilt. In den Proben, die mit 620 und 650 Grad behandelt wurden, entmischen sich die Elemente allmählich. Es entstehen Bereiche mit jeweils mehr Eisen, Chrom oder Molybdän. Dabei bilden sich zunehmend kristalline Strukturen. Eine mit 800 Grad Celsius behandelte Probe ist völlig kristallin, wobei die mit jeweils einem Element angereicherten Areale bis zu 50 Nanometer groß sein können. Das beeinflusst die Nanostruktur stark und damit die Korrosionsbeständigkeit des Stahls.
Quelle: MPI für Eisenforschung
Mit Hilfe der Atomsonden-Tomografie untersuchten die Wissenschaftler die Stahl-Varianten und entdeckten die unterschiedlichen Strukturen im Stahl je nach Herstellungstemperatur. Die Probe, die von den Materialwissenschaftlern bei 620 Grad Celsius erzeugt wurde, blieb noch weitgehend ungeordnet. „Doch auch in dieser Probe lassen sich bereits kristalline Strukturen erkennen“, so die Materialforscherin Jazmin Duarte. „Die bei 800 Grad erzeugte Form ist dagegen völlig kristallin, wobei sich die jeweils mit einem Metall angereicherten Bereiche über bis zu 50 Nanometer ausdehnen können.“
Amorphe Stähle schützen sich durch eine Oxidschicht
Um das Korrosionsverhalten zu untersuchen, wurden die Oberflächen der Probelegierungen mit einer Salzlösung benetzt und unter elektrische Spannung gesetzt. „Dabei erwiesen sich die völlig und die weitgehend amorphe Form als fast so beständig wie reines Chrom“, erklärt Julia Klemm, die die entsprechenden Experimente durchgeführt hat. Reinem Chrom kann die Korrosion unter normalen Bedingungen wenig anhaben, weil es durch eine dünne passivierende Oxidschicht versiegelt wird. Eine solche Schutzschicht bildet sich aber auch auf den amorphen Stählen. In den größtenteils kristallinen Formen der Legierung ist das aber offenbar nicht mehr möglich. Hier frisst der Rost schon bei relativ niedrigen Spannungen Löcher in die Probe.
„Dass sich aus unserer Modell-Legierung elektrochemisch poröse Strukturen der sehr harten Verbindung aus Eisen, Chrom und Kohlenstoff erzeugen lassen, haben wir eher zufällig entdeckt“, sagt Studienleiter Renner. „Wegen ihrer sehr großen Oberfläche könnten sie sich als Membranen für Filter oder Trägermaterialien für Katalysatoren eignen.“ Denn sowohl Filter als auch Katalysatoren erfüllen ihre Aufgabe desto besser, je größer ihre aktive Oberfläche ist. Für Karosserien, Flugzeugrümpfe oder Turbinenschaufeln ist ein kristalliner Chrom-Molybdän-Stahl, den der Rost perforiert, dagegen unbrauchbar, so die Forscher.
Amorphe Stähle schon mit 5 % Chrom korrosionsbeständig
Der Zusammenhang zwischen Chrom-Verteilung und Korrosionsschutz gibt den Materialwissenschaftlern auch einen Hinweis, warum amorphe Stähle bereits durch einem Chrom-Anteil von vier bis fünf Prozent korrosionsbeständig werden, während dafür in kristallinen Stählen 12 bis 13 Prozent nötig sind: Letztere müssen insgesamt mehr Chrom enthalten, damit auch in den chromärmeren Kristalliten genug vorhanden ist, um die passivierende Schicht über dem gesamten Material zu bilden.
Zwar können die Forscher noch keine Rezepte an die Industrie melden, aber erste Hinweise geben, wie rostbeständigerer Stahl hergestellt werden kann. „Unsere Studie zeigt, dass bereits die Entmischung im Nanometerbereich stark beeinflusst, wie korrosionsbeständig ein Material ist“, so Renner. Dass sich alle Komponenten möglichst gleichmäßig in einem Material verteilen sollten, damit der Rost es nicht zerfrisst, könnte also ein Anhaltspunkt für die praktische Materialwissenschaft sein.
Ein Beitrag von: