Zerspaner nehmen CFK ins Visier
Automatisierte Fertigungsprozesse könnten die Produktion von Bauteilen aus CFK erleichtern – und deren Preise senken. Um realitätsnah simulieren zu können, benötigen die Softwareanbieter aber ein Werkstoffmodell, das die Besonderheiten der Kohlenstofffaser berücksichtigt. Das wird auf der morgen endenden Fachmesse für Metallbearbeitung AMB in Stuttgart deutlich.
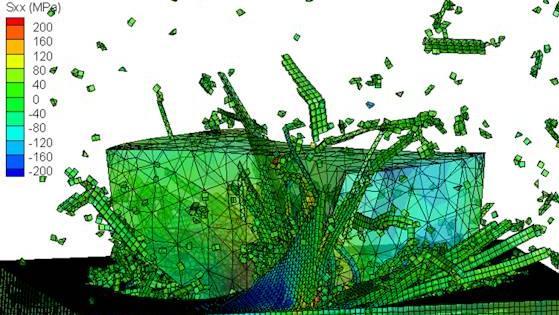
Softwarehersteller zeigen, wie sie die Zerspanung von CFK vereinfachen wollen.
Foto: Werkfoto
So sehr die Konstrukteure auch die Kohlenstofffaserverstärkten Verbundwerkstoffe (CFK) lieben, die Fertigungstechniker stehen mit dem „besseren Metall“ mitunter auf Kriegsfuß. Vorzüge wie Festigkeit, Leichtigkeit und Ausdauer verlangen ihren Preis – nicht nur monetär. Der spröde CFK gehorcht bei der Zerspanung nicht den aus der Metallurgie bekannten Gesetzen und zwingt die Ingenieure dazu, längst beherrschte Fertigungsprozesse neu auszuloten.
Auch die morgen endende Internationale Ausstellung für Metallbearbeitung AMB kommt an diesem zutiefst nichtmetallischen Thema nicht vorbei. Softwarehersteller zeigen in Stuttgart, wie sie die Zerspanung von CFK mit Simulationspaketen vereinfachen wollen. Im Kern aller Lösungen steht das Werkstoffmodell.
CFK lässt sich nicht in alle Richtungen gleich gut zerspanen
Der Wissenstransfer aus der Metallbearbeitung trägt die Modellierer nicht weit, denn der typisch metallischen Isotropie steht beim CFK Orthotropie gegenüber. Die Materialeigenschaften hängen von der Richtung im Bauteil ab – mit Folgen für die spanende Fertigung. „CFK verhält sich – je nachdem, in welchem Winkel zur Faser der Schneidkeil eingreift – vollkommen unterschiedlich. Der Werkstoff lässt sich nicht in allen Richtungen gleich gut zerspanen“, erläutert Kay Marschalkowski, Leiter des Unnaer Tool Engineering Center von ISBE, Stuttgart.
Auch der Verbundcharakter macht den Zerspanern Schwierigkeiten – hochfeste Kohlenstofffasern wechseln sich mit der weichen Matrix ab. Zusätzlich setzen viele Verarbeiter in der Praxis auf Gelege, deren einzelne Schichten unterschiedlich orientiert verlaufen.
Thomas Bruchhaus, bei Sandvik Coromant in Düsseldorf für Bohrwerkzeuge zuständig, betont eine weitere Schwierigkeit: „Die Herausforderung sehe ich heute darin, dass Bauteile aus Schichten völlig unterschiedlicher Materialien bestehen, dass etwa CFK in Kombination mit Titan und Aluminium vorliegt.“ In diesem Materialmix sieht er die „Meisterprüfung“ eines Werkzeugs.
Die Belastungen im Werkzeug sind allerdings nicht das größte Problem, gut ausgelegt erreichen sie gute Standzeiten und Zerspanleistungen. Hochfeste Beschichtungen aus Diamant schützen Bohr- und Fräsköpfe.
Das Problem liegt vielmehr auf der Werkstückseite. Bruchhaus unterscheidet beim Bohren insbesondere zwei Materialschädigungen. Erstens können einzelne Fasern, die beim Bohren nicht richtig getrennt wurden, zurückfedern und die Montage eines Niets blockieren. Zweitens können Delaminationseffekte auftreten: Die CFK-Schichten trennen sich.
Auch Marschalkowski berichtet von unsauberen Schnittkanten an der Bohrungswand sowie am Ein- und Austritt des Bohrers. „Deshalb erreicht man erstens teilweise nicht die geforderten Toleranzen. Zweitens bringt man Vorschädigungen in das Material ein, die wiederum die Festigkeit beeinträchtigen“, sagt der Experte für Zerspantechnik. Sein Fazit: „Die Qualität lässt oft zu wünschen übrig, weil sie nicht zu 100 % durch den Zerspanprozess kontrollierbar ist.“
Werkzeugmaschinenhersteller im Kampf gegen CFK-Stäbe
Und auch die Werkzeugmaschinenhersteller befassen sich zunehmend mit CFK. Der Grund: Späne, genauer CFK-Stäube, dringen hinter die Maschinenverkleidungen, setzen sich auf Führungen und Antriebe und führen dort zu abrasivem Verschleiß. „Spezielle Abdeckungen können nur die größeren Späne fernhalten“, erklärt Heiner Lang, Entwicklungschef beim Werkzeugmaschinenbauer MAG, Göppingen. In gekapselten Systemen sorge aber ein gezielter Überdruck für Reinheit.
Der Weg zur kontrollierten Zerspanung der Kohlenstofffaser ist weit: Die Ingenieure müssen sowohl die optimalen Werkzeuggeometrien als auch die richtigen Prozessparameter finden. Allein die Werkzeugherstellung verläuft in zahlreichen Iterationsschritten. Simulationen machen Feldversuche zwar nicht überflüssig, verringern aber deren Anzahl. „Wir verlagern einen Teil der Versuche in den virtuellen Raum, um den Maschinenaufwand erheblich zu verringern und um Maschinenzyklen freier und auf einer breiteren Basis durchspielen zu können“, fasst Marschalkowski zusammen.
Er baut auf die Finite Elemente-Methode (FEM), die auf physikalischen Prinzipien beruht. „Wir nutzen weniger analytische bzw. empirische Modelle, sondern vielmehr physikalische Gesetzmäßigkeiten“, sagt der Experte für Zerspantechnik. Dies biete einerseits die besten Möglichkeiten, „realitätsnahe Ergebnisse“ zu erzielen, mache die FEM andererseits aber zu einer hochkomplexen Methode, die eine genaue Kenntnis der Prozesse voraussetze.
Die gründliche Modellierung der CFK-Zerspanungsprozesse ist „Pionierarbeit“
Den Softwareentwicklern bleibt noch viel Arbeit, ehe die Prozesse bei der CFK-Zerspanung gründlich modelliert sind. Für Marschalkowski ist das „Pionierarbeit“. „Nachdem wir ein erstes Materialmodell für Gelege entwickelt haben, müssen nun spezifische Modelle folgen“, sagt der Werkzeugingenieur. Als Treiber der Entwicklungen in der Simulationstechnik nennt er die Flugzeugbauer Airbus und Boeing sowie den schwedischen Werkzeugbauer Sandvik, perspektivisch aber auch die Automobilindustrie.
Für die Anwender verheißen solche Modelle die Möglichkeit, viel Zeit zu sparen. Aus der Metallbearbeitung etwa sind Fälle bekannt, in denen der Kreis von 40 möglichen Prototypen durch Simulation auf unter 10 reduziert wurde.
Ein Beitrag von: