Marode Autobahnbrücken schneller sanieren
In Deutschland sind rund 8000 Autobahnbrücken sanierungsbedürftig. Diamant Polymer antwortet mit einem speziellen Spaltausgleichsmaterial.
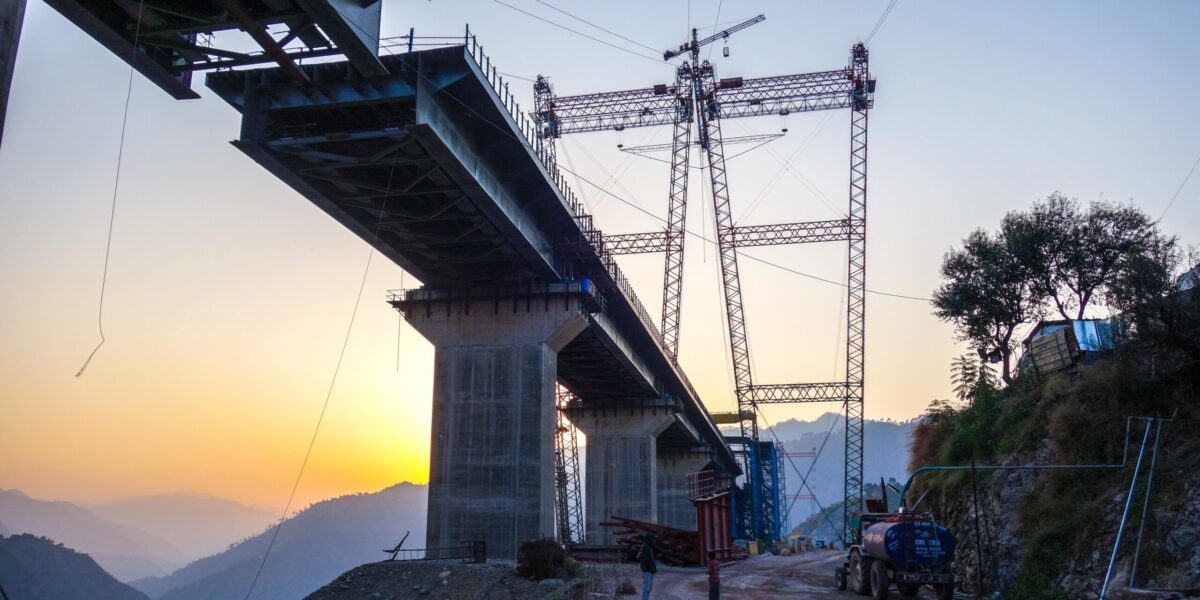
Das flüssige Futterblech von Diamant Polymer aus dem niederrheinischen Mönchengladbach kam auch bei der Chenab-Brücke in Indien zum Einsatz, der größten Eisenbahnbogenbrücke der Welt. Das Bauwerk überspannt den Fluss Chenab in einer Höhe von 359 m.
Foto: Diamant Polymer
Der Einsturz der Carolabrücke in Dresden hat ein heißes Thema auf den Tisch gebracht: Deutschlands Autobrücken sind in einem dramatischen Zustand, besonders in Westdeutschland, wo viele Brücken aus den 1960er- und 1970-Jahren deutliche Alterserscheinungen zeigen. Das Verkehrsministerium geht davon aus, dass rund 8000 Brücken bundesweit eine Sanierung benötigen – jeweils 4000 Bauwerke in einem Zeitraum von zehn Jahren. Ausgebremst wird die Modernisierung allerdings durch hohen Fachkräftemangel, hohe Rohstoffpreise und gestiegene Baukosten.
Flüssiges Futterblech gleicht Spalten aus
Entsprechend hilfreich sind Technologien, die die Brückensanierung effizienter machen. Ein Unternehmen, das in diesem Bereich eine Lösung anbietet, ist die Diamant Polymer GmbH aus Mönchengladbach. Als Spezialist für Polymerchemie entwickelt das Unternehmen duroplastische, selbstaushärtende Kunststoffe zur Reparatur, zum Schutz und zur Optimierung von Metall- und Maschinenbauteilen in der Industrie. „Ein wichtiges Produkt für die Brückensanierung ist das sogenannte flüssige Futterblech MM1018 – ein Spaltausgleichsmaterial, das in kurzer Zeit eine kraft- und formschlüssige Verbindung zwischen Stahlbauteilen herstellt“, sagt Carsten Kunde, Inhaber und Geschäftsführer der Diamant Polymer GmbH. „Es ist derzeit in Deutschland das einzige Spaltausgleichsmaterial für Stahlbauteile mit einer bauaufsichtlichen Zulassung vom Deutschen Institut für Bautechnik.“
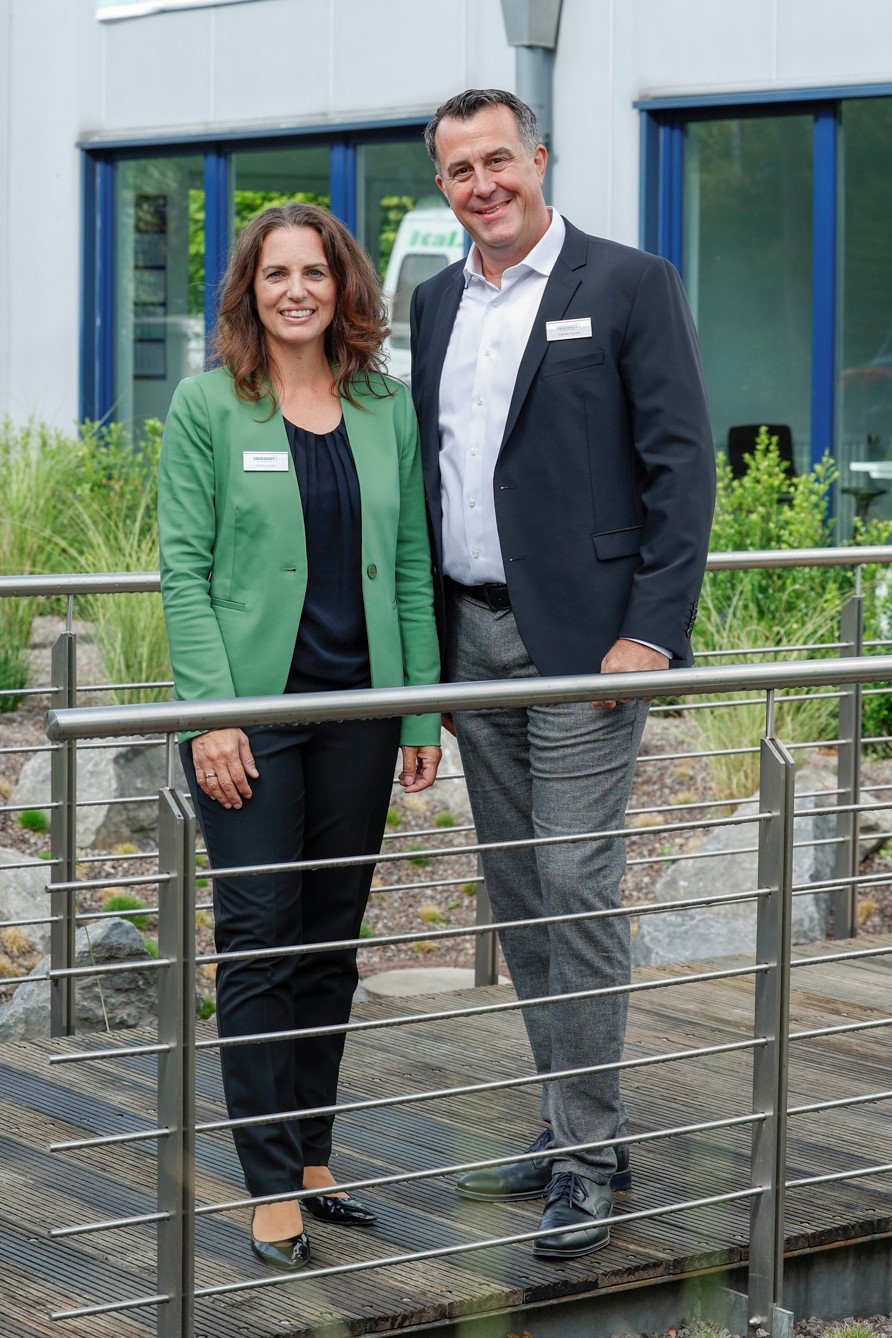
Das Geschäftsführungsduo der Diamant Polymer GmbH: Sandra Pinter und Carsten Kunde.
Foto: Diamant Polymer
Das flüssige Futterblech kommt bei der Brückensanierung unter anderem beim Austausch von Brückenlagern zum Einsatz. Diese tonnenschweren Bauteile übertragen das Gewicht der Fahrbahn auf die Pfeiler und Fundamente. Gleichzeitig sorgen sie dafür, dass die Fahrbahn flexibel schwimmt, um Verformungen auszugleichen und Schäden zu vermeiden.
Lesetipp: Ultraschall erhöht Sicherheit bei Stahlbeton
Dafür sind die Lager zwischen dem Pfeiler und dem Stahluntergurt der Brücke positioniert. Ihr Austausch ist allerdings aufwendig. Denn die Oberfläche des Untergurts wird im Laufe der Zeit leicht uneben – bedingt durch altersbedingte Abnutzung, Frost-Tau-Wechsel und Feuchtigkeit. Diese Unebenheiten gilt es vor der Montage neuer Lager auszugleichen, um eine gleichmäßige Lastübertragung zu gewährleisten. Andernfalls könnten die Lager schnell zerstört werden. „Die unebene Oberfläche des Stahluntergurts mechanisch zu bearbeiten oder passgenaue Futterplatten anzufertigen, ist zeitaufwendig und entsprechend unbeliebt“, sagt Kunde. Das Unternehmen habe deshalb als Alternative das flüssige Futterblech entwickelt.
Das Geheimnis: Polymere mit Füllstoffen
Das Material – eine geheime Kombination aus Polymeren und Füllstoffen – wird zwischen den Stahloberflächen von Lager und Brücke angewendet und lässt sich in Ritzen und Vertiefungen einbringen, um eine gleichmäßige und stabile Fläche zu schaffen. Nach der Montage des Lagers am Stahluntergurt härtet das Material dann eigenständig chemisch aus und nimmt dabei eine dauerhafte, unveränderliche Struktur an, die für eine optimale Kraftübertragung sorgt. Das flüssige Futterblech erreicht dabei mit bis zu 160 N/mm2 eine rund vierfach höhere Druckfestigkeit als Beton.
„Neue Brückenlager lassen sich mit diesem System unkompliziert einbauen“, sagt Kunde. „Die Lösung ist somit ein weiteres Puzzlestück, um kostengünstige und schnelle Instandsetzungen von Brücken zu ermöglichen und so den erheblichen Sanierungsstau zu bewältigen.“ Zum Einsatz käme das flüssige Futterblech mittlerweile weltweit – unter anderem auch an der Chenab-Brücke in Indien, die größte Eisenbahnbogenbrücke der Welt, die den Fluss Chenab in einer Höhe von 359 m überspannt.
Die Geschichte von Diamant Polymer reicht zurück ins Jahr 1886. Damals gründete Robert Schulz in Rheydt eine Drogerie. Heute ist das Unternehmen in fünfter Generation, geführt von Sandra Pinter und Carsten Kunde, und fokussiert sich unter anderem auf die Entwicklung von hochviskosen Produkten.
Lesetipp: So werden Brücken in Deutschland geprüft
Das grundlegende Prinzip ist stets dasselbe: Die Materialexperten kombinieren Polymer als Trägermaterial mit funktionalen Füllstoffen, sodass sich spezifische Materialeigenschaften ergeben – etwa Leitfähigkeit, Hitzebeständigkeit oder eine hohe Gleitfähigkeit. Die Produkte finden vielfältige Anwendungen, beispielsweise beim Bau von Werkzeugmaschinen und Bearbeitungszentren, um hochpräzise Gleitflächen ohne mechanische Bearbeitung herzustellen. Kunde: „Das spart nicht nur Zeit und Kosten, sondern ist auch nachhaltig, da weder Energie aufgewendet wird noch Materialverlust durch die Bearbeitung entsteht.“
Im Sortiment der Mönchengladbacher finden sich darüber hinaus auch niedrigviskose Lösungen. Dazu zählt beispielsweise ein lösemittelfreies Hochleistungspolymer, das als sprühbares Imprägniermittel für Objekte aus dem 3D-Drucker zum Einsatz kommt. Es kann beispielsweise in einer gedruckten Blumenvase Poren bis 0,2 mm gas- und wasserdicht machen. Diese Systeme existieren mittlerweile in mehr als 60 Varianten und sind ebenfalls in der Luft- und Raumfahrtindustrie zu finden. Dort werden leichte Aluminiumwerkstoffe beim thermischen Spritzgießen mit einer verschleißfesten Keramikbeschichtung ummantelt, um die Verschleißfestigkeit zu erhöhen. Die Imprägniermittel schließen hier die Mikroporen in der Beschichtung und machen diese dauerhaft haltbar.
Bis heute formuliert, entwickelt und produziert Diamant Polymer ausschließlich am Standort Deutschland. „Hierzulande sind wir gut aufgestellt. Wir wollen unsere Produkte, mit denen wir sehr innovative Märkte im Blick haben, deshalb in Zukunft vermehrt im Ausland zum Einsatz bringen“, so Kunde abschließend. „Wir haben Joint Ventures in Indonesien und Indien sowie Anfang des Jahres eine Niederlassung in den USA gegründet.“
Ein Beitrag von: